Alle platen op het platenpark gingen vroeg of laat via het planeergebouw de werf rond. In dit gebouw, dat ook de administratie ijzermagazijn herbergde, werden de platen gecontroleerd op luchtbellen en op rechtheid. Na de start ging het naar het ontroestergebouw.
De ontroester deed wat de naam zegt en bij het verlaten van de ‘grenailleuse’ werden de platen voorzien van hun eerste verflaag. De platen werden genummerd en ofwel naar de Wagner plaatschaar, de kleine brandtafels of de brandmachines gebracht door de hefbruggen of rolbanen.
Huid of schotplaten werden verder doorgevoerd naar de duwmachines zoals de grote en kleine Bakkers en de Wilhelmsburger.
Ten slotte ging het naar de montagehallen waar platen, en stukjes ervan, werden samen gebouwd tot secties.
Vooraleer de platen konden bewerkt worden, dienden ze eerst de werf te bereiken.
De mensen die allereerst met de platen in aanraking kwamen, behoorden tot de losploeg. Zulk een losploeg op de kade van Temse bestond gewoonlijk uit 5 man. Twee man die de plaat aanpikten in het ruim van het binnenschip en twee man op de kade die de plaat losten. De chauffeur was de vijfde man, hij reed heen weer tussen het de kade en het platenpark. Bij regenweer was het ondankbaar werken op de kade. Door de slechte waterafvoer en het achtergebleven zand van schepen met bouwmaterialen die daar gelost werden, was het soms ploeteren door een ware modderbrij. Omdat alle 8 lossers echter graag naar de kade trokken ter afwisseling op het werk, moest de brigadier een beurtrol inschakelen.
De platen werden aan wal gebracht door twee kraantjes van de firma Van Riet. Om de platen naar het platenpark te brengen maakte men gebruik van drie platte wagens, nog afkomstig van de ‘Stock Americain’. Een wagen die geladen wordt op de kade (40 ton per keer), een wagen die gelost wordt in het platenpark en een wagen in beweging. Van de losploeg was enkel de chauffeur de vaste man.
![]() |
Type platte wagen, restant van het Amerikaanse Leger na WOII, veelvuldig gebruikt op de werf. |
![]() |
De combinatie DiamondT Model 981 met M9 Rogers aanhangwagen. |
De vier kleine Belgomine kraantjes werden in de jaren 1980 vervangen door twee grotere. Een ervan werd aangepast zodat er een zwengel met zuignappen aan de haak kon gehangen worden. Met die vacuüm zuignappen was het makkelijker om platen, weliswaar een voor een, te tillen. Er was nog steeds volk nodig in het ruim, dit om het vuil en stof weg te vegen zodat de nappen goed vacuüm konden trekken. Maar het ging sneller en veiliger.
- Planeergebouw voorraan
Alle platen die in productie kwamen werden eerst nagekeken op inwendige luchtbellen en scheurtjes. Een ultrasoon apparaat registreerde deze onregelmatigheden en projecteerde de resultaten op een scherm. Platen met fouten werden teruggestuurd naar de staalfabriek of kregen eventueel een andere bestemming.
De rollen van de planeermachine oefenden een druk uit op de plaat. Deze werd dus vlak gerold. Eens door de machine, werd de identiteit en plaats van bestemming op de plaat aangebracht en vervolgde ze via de transportband en rolbrug B20 haar weg naar de ‘grenailleuse’.
Achtereenvolgens werd de plaat hier gedroogd, ontroest door middel van metaalkorrels, en geverfd met een speciale samenstelling ‘ecol’ zink.
Na de ontroester werden de platen ofwel doorgestuurd naar de cinema, naar de Wagner of de brandmachines.
Indien er geen verdere bewerkingen nodig waren gingen de platen rechtstreeks naar de voormontage. (Blok I, Blok III, 200ton loods of het half overdekte stockageplein)
In de cinema, gelegen binnen het ontroestatelier, werden via optische afschrijving de kleine stukjes plaat of de openingen met doppen afgetekend, beter bekend als piqués. De mensen die dit werkje uitvoerden konden én goed zien én goed met hamer en dopper overweg.
In het volgende atelier werden die stukjes, zoals knieën en dergelijke, halfautomatisch of handmatig gebrand.
Aan de Wagner, naast de ontroester, werd de plaat op breedte en lengte gesneden en voorzien van een afschuining, nodig om ze samen te lassen met andere platen. De rolschaar was vooral aangeschaft om roestvrijstalen platen op maat te snijden en van afschuining te voorzien. Dit schaartje kon plaatdikte tot 39 mm snijden. De ‘krullen’ of knipresten waren soms amper te tillen.
De brandmachines waren eind jaren zestig semi-geautomatiseerd. De tekening, van de te branden plaat op schaal, lag in een apart lokaal met uitzicht op de branderstafels. Een lichtpen volgde de lijn op het plan en stuurde de signalen naar de branderskoppen. Dit ging uiteraard veel vlugger dan het branden met de hand. Er was wel een strikte controle nodig of de afmetingen wel correct waren. Hiervoor kwam de kwaliteitsdienst regelmatig, meermaals daags, de platen nameten. De controle was zowel lengte, breedte als diagonaal.
Een volgende generatie machines werden computergestuurd. Het signaal voor de snijkoppen werd met computertaal overgebracht. Dit ging sneller en accurater. Maar toch was er nog steeds heel wat werk, alleen was een deel overgebracht naar de computerafdeling van de werf. En het grote nadeel na het branden bleef, bramen. Deze moesten uiteraard verwijderd worden om later een mooie en sterke las te kunnen verkrijgen. Aan de brandmachines werd in twee (soms drie) ploegenstelsel gewerkt.
Midden de jaren zeventig, na de oliecrisis, werd gedacht om deze productie wijze te verbeteren. Hiervoor kreeg de afdeling ontwerp in 1978 volgende opdracht: de snijcapaciteit vergroten met het oog op veiligheid en milieu.
Roger Vyt, die de dienst investeringen leidde, vroeg zich af of het mogelijk was om te snijden zonder rook- en metaalspatten. De conventionele gassen zouden hiervoor minder geschikt zijn. Na prospectie van de markt bleek dat plasma een mogelijkheid was. Het project PLASMA ONDERWATERSNIJDEN was geboren. De te ontwerpen brandmachine moest ook lijnmarkeren aankunnen (zie cinema en piqueren). Het onderdompelen en droog zetten van de plaat diende vlug te kunnen gebeuren. Een bijkomend aspect was besparing, dus één-man bediening.
Een dergelijke machine bestond niet! Wel waren er in laboratoria en teststations al enkele proeven met plasma uitgevoerd. Van onderwatersnijden was echter nog geen sprake.
Na vele besprekingen en heel wat testen kon de ontwikkeling van dergelijke machine een aanvang nemen. Na het fiat van hogerhand werd een installatie getekend en een prijsvraag bij twee geïnteresseerde firma’s geplaatst. Fase I was achter de rug.
Fase II verliep dan in samenwerking met Messer. Vele obstakels dienden te worden geruimd. Zo was er het probleem van het water. Op welke manier kon men dit proces van het onderwater zetten en terug droog maken op een snelle manier laten verlopen.
Roger zijn dienst bedacht hiervoor een oplossing. Het snijbed werd op een luchtklok geplaatst die op zijn beurt in een kuip stond. Door perslucht in de klok te blazen kwam het water op enkele seconden omhoog. De fabrikant van de brandmachine moest het bedieningsbord zodanig ontwerpen dat alle functies vanuit één punt konden gestuurd worden.
Later werd, in Fase III, met de tekenkamer afgesproken dat alle nieuwe (computer) codes in het bestaande Boelwerf-systeem zouden worden geïntegreerd.
Bijna twee jaar later, maart 1980, kon fase IV een aanvang nemen: montage en testen van het geheel. Mensen uit de onderhoud werden hierbij actief betrokken.
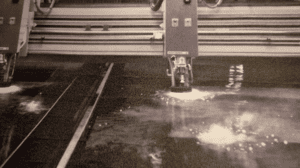
Tweemaal jaarlijks diende het pinnenbed, het water en de luchtklok verwijderd te worden om het ‘slib’ uit de kuip te halen

Optimaal benutte plaat, de onderdelen konden tot verschillende secties behoren
In het atelier plaatbewerking, vooraan de werf, werden de platen gevormd met behulp van duwmachines, de Bakkers. Met mallen werden de krommingen nagekeken. De bewerkte platen gingen dan op een buizenstoel om de juistheid en het aansluiten op de volgende plaat te controleren.
De Willemsburger had een groot bed waar platen over volle lengte (12m) onder de pers konden. De wafelvorm voor o.a. de tussenschotten werd hier met tweeduizend ton duwvermogen uitgevoerd.
Een volgende halte voor platen en knieën, stuiken enzoverder was de stockage voor Blok III, waar de halfportiek B43 actief was. Die stockage plaats was niet toevallig gekozen want aansluitend aan de paneelstraat. Via een transportband worden de platen Blok III binnen gerold en met een vacuüm balk op station I gelegd.
Op Station I werden tot maximum 5 platen aan elkaar gelast. Het keren van zulk een vlak van ongeveer 12 op 11 meter was steeds spectaculair. Het gekeerde platenvlak werd op Station II gelegd voor een tegenlas. Evenals in station I werd deze las gelegd met de automatische tandem lasmachine.
Een ultrasone controle van de lassen werd dan ook uitgevoerd, zeker voor huidplaten.Het op maat brengen gebeurde op Station III. De plaatsen waar bulben en profielen moesten komen werden hier afgeschreven en het definitief sectienummer werd aangebracht.
Het volgende Station IV was de vacuümblast. Doormiddel van zandkorrels werd zeer plaatselijk de verf verwijderd, op de plaats dus waar die profielen dienden te komen. Dit station was verdeeld op twee niveaus. Beneden lag de plaat met de strepen en boven werden de opstaande kanten van de profielen eveneens gezandstraalt. Die profielen werden dan op de plaat neergelaten en met een cilinder stevig aangedrukt en vast gezet met een speetlas.
Als laatste Station V werden de profielen en bulben met de duomatic afgelast.
De paneelstraat werd in 1972 in gebruik genomen en was een revolutionair systeem voor het samenstellen van vlakke secties. Voorheen lagen in dit deel van Blok III de hellingen 5 en 6.
De volgende halte van deze vlakke plaatsecties waren de montagehallen. Samen met andere wanden konden secties worden gevormd tussen 50 en 200 ton.
Op de pleinen rond het dok werden grotere secties samengesteld, tot wel 6 à 700 ton.
Uiteraard is een schip veel meer dan een stalen plaat. Nochtans zijn de huidplaten het belangrijkste om een zeereus drijvende te houden.
Tekst: Hugo Van Britsom
Nalezing door Marc Hauman, waarvoor dank.
Met dank aan Roger Vyt voor de informatie in verband met de plasmabrandmachine.